KODA AUTO is experimenting with HoloLens augmented reality headsets to support production line maintenance. Documentation including maintenance checklists and manuals can be displayed as holographic images into the wearer’s immediate field of vision. The view through the AR glasses can also be shared during video conferences and used for training purposes.
Head of Brand Management at ŠKODA AUTO, Miroslav Kroupa explained:
“As part of our current pilot project, we are relying on augmented reality to optimise the maintenance and repair of our machines and to minimise the error rate. With the HoloLens glasses, our technicians have all the relevant information at a glance at all times and can concentrate fully on their work at the same time. In this way, the AR glasses help to further increase work safety.
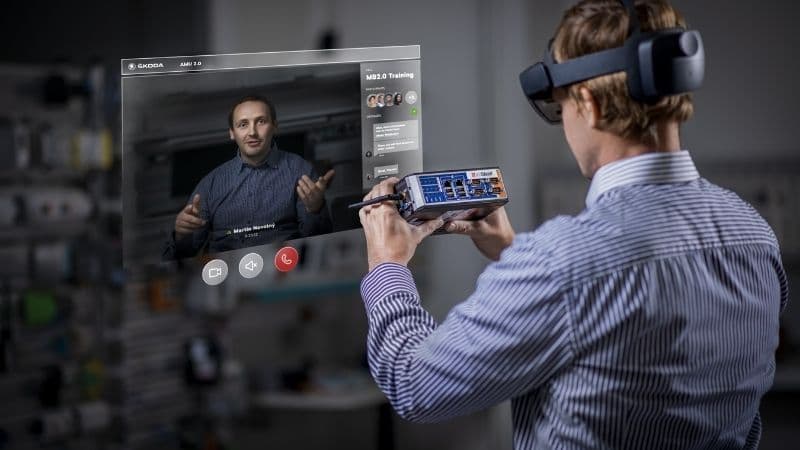
Kroupa continued:
“The tool makes it possible to exchange information flexibly anywhere and at any time, even with colleagues at other locations or in different time zones. This speeds up maintenance processes significantly and is an enormous advantage, especially in times of the COVID-19 pandemic. Furthermore, the glasses add gamification elements to everyday work and inspire young candidates for technical professions.”
ŠKODA AUTO’s Central Technical Service department and the ŠKODA AUTO FabLab are the first sectors to experiment with augmented reality technologies in production line maintenance as part of a pilot project.
Technicians wearing the HoloLens glasses can connect to video calls to show what they see on the line and consult with colleagues who are not on site. The glasses can also be used to share technical files and other documents.
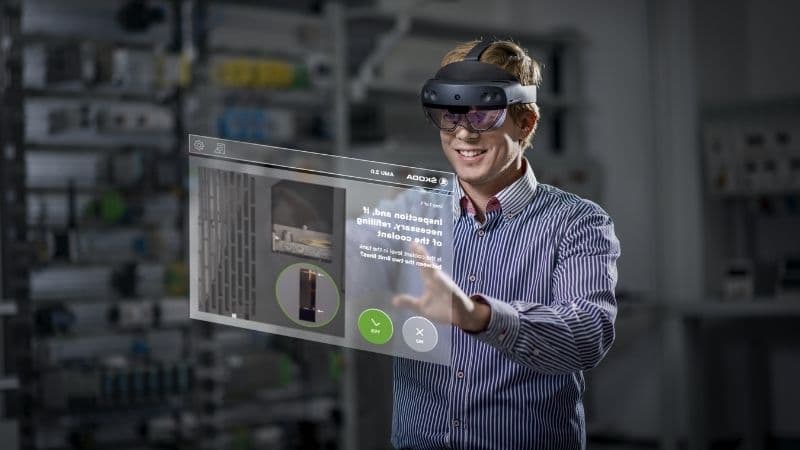
The HoloLens augmented reality glasses can display information from instructions, checklists and manuals during technical maintenance. To access that information, staff simply scan a QR code on the respective equipment which is embedded with the correct documentation in an interactive guide which directs the wearer through the maintenance work step by step with photos and videos, among other things. This allows the technicians to be hands-free at all times to complete the task. Once the task has been completed, the technician ticks it off with a hand movement in the hologram.
Utilising augmented reality technology reduces the chances of technicians making errors and enables service intervals to be carried out on a more flexible basis, quickening the maintenance process. Any remaining service requirements are recorded on the internal system via the Wi-Fi connection. HoloLens glasses also make repair work much easier with the help of video instructions, making it no longer necessary to refer to bulky technical manuals.